Understanding pressure and flow
When discussing compressed air systems, pressure and flow are integral parts of how a system will utilise the air.
Let’s dive into the difference between the two and the nature of the relationship between pressure and rate of flow within a compressed air system.
What is pressure?
Pressure is the measure of force that’s applied to an area and determines the compressor’s ability to perform a specified amount of work at any given point in time. Each pneumatically powered device has a stated pressure range in which it works reliably, and these limits must not be exceeded.
Pressure, typically measured in pounds per square inch (psi), determines the system’s ability to perform a certain amount of work at any given point in time. To check the PSI of your existing system, look at the air gauge on the air compressor – this is where the system pressure will be displayed.
What is flow?
As a measure of volume, flow indicates a system’s output rate. The length of time to complete the task is what will determine the amount of airflow. A compressor will need to stop and rebuild pressure in the tank if it does not have sufficient flow for the job. Flow is typically measured in cubic feet per minute (cfm) at a specific pressure. The amount of flow depends on the length of time needed to complete the task.
How do pressure and flow work together?
Air pressure and flow have a unique relationship. When using a compressed air system, the goal is to supply the proper airflow at the correct pressure. It is imperative to know the minimum pressure needed to complete a task. A slow increase in pressure is always best so as not to waste energy.
As for airflow, it will take into consideration how often the task is completed. For example, let’s say you need to move something a short distance every hour with a compressed air system. This task will only require the use of a small compressor. However, if the task requires constant movement for several hours, then a larger compressor is required.
In a compressed air system, the amount of pressure has a direct impact on the rate of flow. According to Boyle’s law, which states:
P1 X V1 = P2 X V2
(where P1 is the initial pressure, V1 is the initial volume, P2 and V2 are final pressure and final volume, respectively), gas pressure increases in inverse relation to the volume of its container.
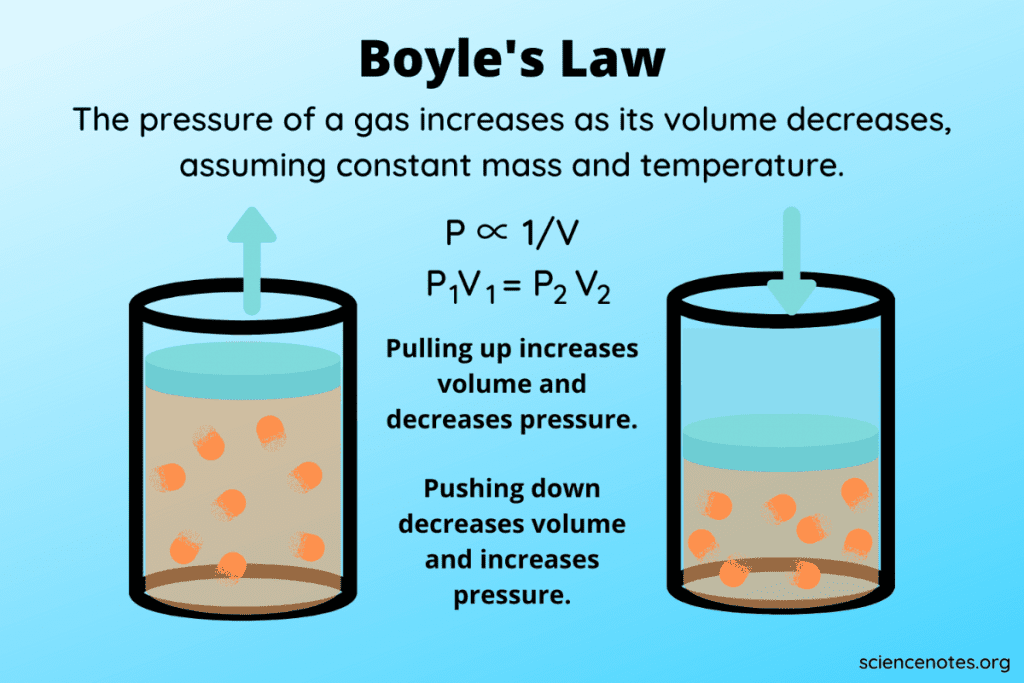
BOYLE’S LAW states that the pressure of an ideal gas is inversely proportional to the volume under conditions of constant mass and temperature. When the gas volume increases, pressure decreases. When the volume decreases, pressure increases. Boyle’s law takes its name from chemist and physicist Robert Boyle, who published the law in 1862.
Overpressurisation
When the psi is increased at the pump and not regulated directly after the air tank, it increases energy costs and loss. Increased pressure also causes leaks. Some of the costliest leaks are those found near the compressor because that is where pressure is highest. Also, a system that is left pressurised when not in use can cause leaks.
Terminology
PSI – This measures the amount of pressure per square inch. For a compressor, it is the amount of force it can deliver.
CFM – The flow rate of a compressor. The amount of air a compressor can produce at a given level of pressure.
HP – The horsepower is the amount of work performed by a compressor’s motor.